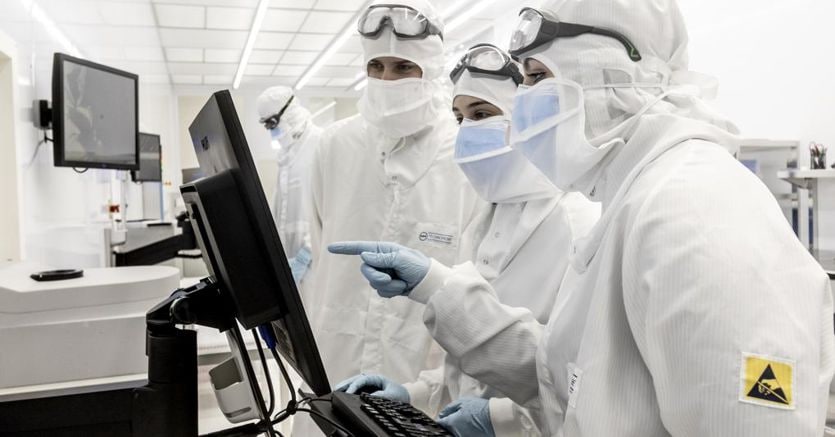
Technoprobe, l’intelligenza artificiale per testare i super-chip
«Fai attenzione, se inciampi e ti cade “fai fuori” un appartamento». Una battuta, quella che circola lungo le linee di assemblaggio, ma fino ad un certo punto. Perché maneggiando le schede di test prodotte da Technoprobe, i tecnici del gruppo hi-tech lombardo si trovano in effetti sul palmo di mano oggetti da centinaia di migliaia di euro, la frontiera della tecnologia per quanto riguarda gli strumenti di test dei circuiti dell’elettronica globale. Dove in particolare è in crescita vertiginosa il segmento dei chip iperveloci, 22 miliardi di dollari che in cinque anni diventeranno nelle previsioni almeno il quadruplo.
«Tra i trend più dirompenti – spiega il vicepresidente per il centro di eccellenza del gruppo Davide Appello – c’è senz’altro lo sviluppo di microprocessori di grande potenza, quelli che consentono la diffusione dell’intelligenza artificiale. E in quel segmento abbiamo in effetti dei volumi in forte progresso». In un certo senso, dunque, algoritmi e schemi di apprendimento evoluti creati grazie ai chip di NVidia o di altri big dei microprocessori, sono in parte made in Cernusco Lombardone (Lecco), sede principale della multinazionale lombarda che dopo la quotazione in Borsa ha raggiunto una capitalizzazione stellare da 4,5 miliardi, realizzando oltre 400 milioni di ricavi lo scorso anno.
Cifra legata al business di nicchia presidiato, schede di test che analizzano rapidamente i contatti dei chip lungo le linee di assemblaggio per anticipare errori ed eliminare oggetti difettosi.
«In pochi millimetri quadrati – spiega Appello – i processori più avanzati presentano anche 100mila contatti. Ma la difficoltà con i chip dedicati all’intelligenza artificiale è anche legata alla quantità di potenza coinvolta, che deve essere dissipata senza danni. Ecco perché mettendo insieme potenza, corrente e densità, dobbiamo affrontare sfide tecnologiche non banali».
Intelligenza artificiale che il gruppo utilizza però anche direttamente al proprio interno, per migliorare la qualità della produzione e ridurre la difettosità dei prodotti. «L’analisi ottica dei difetti è lo strumento principale – spiega Appello – ma abbiamo deciso di andare oltre l’attività umana, costruendo algoritmi di riconoscimento. In passato si passavano ore ed ore al microscopio, in un lavoro pesante sia dal punto di vista fisico che soprattutto mentale. Adesso il lavoro dell’operatore cambia, perché è l’uomo ad istruire la macchina a riconoscere i problemi, riservandosi quindi l’attività strettamente intellettuale e contribuendo così a ridurre in modo drastico gli errori».
Fonte: Il Sole 24 Ore